ものづくりにおいて、発熱はあらゆる場面で課題となる現象です。これはモータに限りません。機械や電子機器によって、なんらかの処理が行われる際、通常必ず熱が発生します。少し考えてみるだけでも例がたくさん出てきます。
- 電流が流れるだけで、電線内の抵抗値によりエネルギーが消費され熱が発生。
- テレビを点けると、映像を映し出すためのバックライト(LED)が発熱。
- スマホを操作すると、内部でさまざまな計算をするために電流の激しい流れが発生し発熱。
特にモータに関しては、電気エネルギーを運動エネルギーに変換するという機能があり、電気的要因だけではなく、機械的要因での発熱もあります。そのため、状況に応じて熱対策が変わり、複雑な対応が必要になります。熱がたまった状態を継続することは、部品の劣化やパフォーマンスの低下、寿命の低下など、良いことは何もありません。場合によっては、事故につながりかねないことも起き得ます。
モータに求められる要求は年々高まるなか、性能が上がれば発熱量も上がるため、冷却技術も日々進歩してきました。今回はこういったモータの発熱にまつわる話をみていこうと思います。
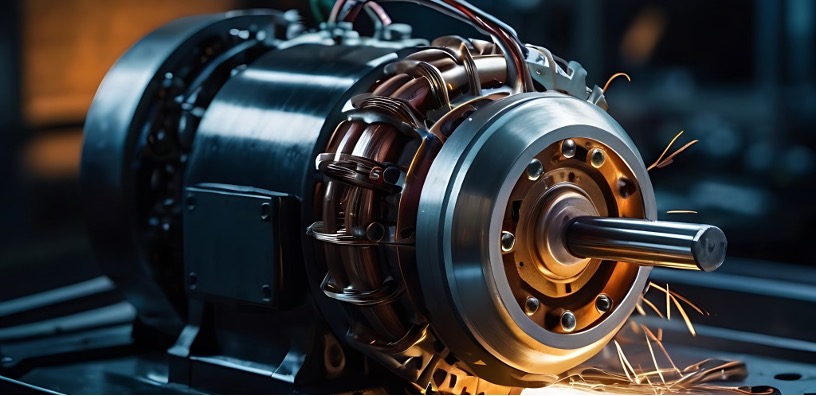
Contents
発熱の主な原因
モータの熱はどこから発生するでしょうか。これは先に挙げた、「電気的要因」と「機械的要因」の2つに大きく分けることができます。具体的にどのようなことが起きているのか、みていきましょう。
電気的要因
銅損(コイルの抵抗による発熱)
モータが回るためにはコイルが必要なのは、皆さんご存じの通りかと思います。コイルは、鉄心に銅線を何重にも巻いて構成されるので、ある程度の抵抗値を持っています。このコイルに電流が流れると、抵抗により熱が発生します。
鉄損(コア内部での損失)
モータ運転時、コイルによる磁場の変化を受け、モータコアに渦電流・ヒステリシス電流というものが流れます。この電流は何か有効な仕事をすることはなく、単純に熱として発散されます。電流の切り替えの回数が早いほど、すなわち回転数が高いほど、この損失は大きくなります。
効率の悪い制御
モータの電力効率は、どんな制御方式を採用しているかによって変動します。モータは電流の流れる方向を常に切り替えながら回転していますが、その切り替えをいかにスムーズに行うかが、電力効率を高める鍵となります。
電流の方向を切り替えるタイミングや、電流出力をどのタイミングでどの程度大きくし、小さくするか。こういった制御をどのように行っているかによって、電力効率は大きく変動します。制御方法が適切でない場合、電力効率が低くなり、発熱を悪化させる要因となります。
ドライバーの性能
モータ単体だけでなく、ドライバーの発熱も忘れてはなりません。ドライバーは、DCブラシレスモータやステッピングモータで必須となるモータを回すために必要となる電子回路のことです。モータ内部に組み込まれる場合も少なくなく、場合によってはモータとセットにした状態で発熱問題を考える必要があります。
電子部品には部品によって発熱が大きいもの小さいもの、発熱に強いもの弱いもの、さまざまな特徴があり、部品の選定が重要です。また、電子基板上の配置問題も忘れてはなりません。限られた面積の中で、全部品を配置するだけでも難しいなか、発熱しやすい部品の近くに熱に弱い部品を配置するなどといったことがないように、レイアウトを検討する必要があります。
苦労して基板設計を完了しても、モータと組み合わせて運転させたときに新たな発熱問題が見つかるといったことも起こり得ます。熱問題は、あらゆる面で配慮しなければならない問題といえます。
機械的要因
軸と軸受けとの摩擦による発熱
回転軸は軸受けと接触しながら回転するため、接触部における摩擦抵抗で熱が発生します。軸受けの種類にもよりますが、潤滑油やグリスが適切に保たれている限りは問題なく、発熱は大きくはなりません。通常使用の範囲では、軸受けにおける摩耗発熱は大きくはなく、発熱が問題になることはまれです。
逆に言うと、何らかの要因で、油が枯渇し油膜がきれてしまったり、異物混入などによって発熱が悪化したりすると、異音発生や摩耗が加速するといった不具合につながります。例えば、モータ内部が異常発熱を起こし、その熱が軸を伝わり軸受けにイレギュラーな熱を与え続けてしまうと、油膜切れを加速させ、軸受けにダメージを与える、ということが起こり得ます。
このように、軸受けの破損原因は別の部品にあるといったこともあるので、不具合調査などの際は注意が必要です。
ブラシ付きモータにおけるブラシ・コミュテータの摩擦熱
ブラシとコミュテータが接触する際、摩擦熱が発生します。高電流、高速回転であればあるほど、熱の発生は大きくなります。高出力で使用する場合は、実使用時の発熱量をきちんと確認し、問題があるレベルであるかどうか、事前に確認しておくことが大切です。ブラシ・コミュテータの摩耗は寿命に直結するため、交換などの管理も重要です。
その他不具合によって引き起こされる発熱
モータの振動によって接触物との摩耗熱の発生、ロータとステータの間の隙間に異物が入るなどによって干渉が発生し、摩耗熱の発生など、不具合によってもイレギュラーな熱は多々発生します。
少し話がズレてしまいますが、そういった不具合事象なども理解しておくと、眼の前の発熱は対策すべきものなのか、それとも発熱を引き起こす別の要因を取り除く必要があるのかなど、正しく判別できます。そのため、不具合事象にも精通しておくと開発、設計、品質保証、製造、全てに役立ちます。
過熱のリスクと影響
熱が無視できないレベルまで上がると、最終的にモータは壊れてしまいます。どのような破壊モードがあるのか、考えてみましょう。
電力効率悪化
この事象は破壊モードではありませんが、大切なことですので、紹介しておきたいと思います。基本的に、電子回路は温度が高いと各抵抗値が上昇します。これにより、消費電力が上がり電力効率悪化。この意味でも、発熱にはメリットがないことがわかります。
コミュテータ・ブラシの摩耗加速(ブラシ付きモータ)
規定の寿命より遥かに早くブラシ交換の時期がきてしまう。
軸受けグリス劣化、油膜切れによる異音、焼き付き
前項でも記載した通り、油膜切れになり、回転時の摩擦がどんどん上昇、摩擦熱により温度が上がり続け、焼き付いて最終的には軸がロックして回らなくなります。
コイルの絶縁劣化によるショート、絶縁破壊
コイルの表面を覆う絶縁被膜が、高すぎる温度に耐えられなくなり溶けてしまいます。結果、コイル間ショートが発生し、モータ内部に大電流が流れ、発熱が悪化。コイルが焼き切れたり、電子部品に大電流が流れたりするなどして回転停止。最悪の場合、火花を発生し、発煙や火災にもつながりかねません。
周囲装置の寿命への影響
モータの発熱は周囲の環境温度を上げることにもなります。そのため、閉じた空間で使われていた場合、想定外の温度上昇を招き、周囲装置の使用温度範囲を超えてしまい、故障させてしまうこともあり得ます。
以上の通り、発熱問題は無視してはならない課題だといえます。
適切な冷却設計のメリット
ここまでの事を踏まえると、冷却設計は非常に大切で、必須なものであるといえます。モータの発熱を適切に抑え、適正温度で使用することにより、下記のメリットが得られます。
- 各部品の劣化スピードが緩やかになり、モータ長寿命化
(ブラシ・コミュテータ・軸受・電子部品など) - モータの電力効率の上昇
- 安全性の向上
- 省エネ
一般的な熱対策(冷却)方法
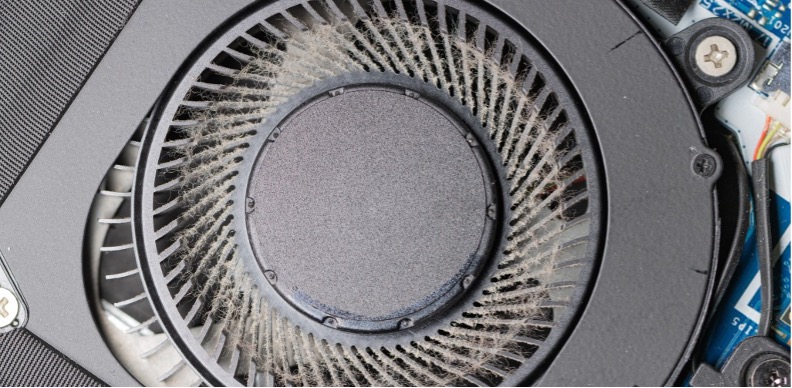
自然冷却(空冷)
特別何か冷やす対処を施すのではなく、空間に熱が逃げるようにスペースを開けるなどの冷却法。開けた空間での使用であれば、この冷却で十分なことも多いです。
強制冷却(空冷)
モータ内外部にファンを取り付け、風の力で冷却する方式です。もっとも一般的な冷却方法であり、冷却といえばこれ、といった印象です。面白いものとしては、モータの出力軸と反対側に小さなプロペラをつけて、出力側で仕事をすると同時にプロペラで冷却を行う構造をもつモータもあります。
水冷(液冷)
空冷よりもさらに強力な冷却方法です。近年はパソコンにも水冷方式が採用されることも増えてきました。この方式は、モータの周囲に熱伝導率の良い金属で水の通り道を張り巡らせるように形成し、金属を通して熱を水に吸収させます。
水は専用のポンプユニットで循環され、ラジエータを通過する際に放熱される仕組みです。非常に放熱性の高いシステムではありますが、冷却システム自体の設計や維持管理の難易度が高く、初期コスト・運用コストも大きいために、冷却に重きを置く限られたモータにのみ適用されている印象です。
オイル冷却(液冷)
こちらは水冷よりもさらに複雑な構造のものです。水冷と同じく液体を用いた冷却方式で、水冷同様高い放熱能力を持っています。水冷と大きく違う点として、油は絶縁性を持たせることが可能な点があります。
これにより、モータ内部に油を流し込み、モータの発熱部位(コイル、コア、磁石など)の熱を直接奪い取る、といった冷却が可能です。しかしながら、モータ内部に油を通すという構造は複雑にならざるを得ません。水冷以上に、構造が複雑になるところが難点です。
ヒートパイプ・冷却フィン・ヒートシンク
これらは、動力を必要としない冷却ツールです。ヒートパイプは、内部に液体が入ったパイプ上の構造をしています。蒸発と凝縮の原理を利用して冷却効果を発現する仕組みです。
パイプの一端を熱源に近づけ、熱を受け取ると内部の液体が熱で蒸発、もう一方の冷たい端へ移動します。そこで冷やされた蒸気は液体に戻り、パイプ内側の壁を伝って蒸発部に戻ります。この循環によって熱の移動を行い、冷却する仕組みです。冷却フィン・ヒートシンクは、魚のヒレのような形をした金属で、冷やす対象の金属に接触させ、表面積を増やすことで熱を空気中に効率的に逃がす効果を持ちます。
モータ種別ごとの冷却方法の選び方
前提として、水冷・オイル冷却は特殊な部類のため、一般的なモータには使われることは、まずありません。出力が高く発熱が大きいとき、もしくは部品の密度が非常に高く、冷却効果を極端に上げないと冷えない場所などで採用されます。
具体的には、水冷・オイル冷却ともに電気自動車用のモータが代表例となります。条件や求められるスペックによって、水冷・オイル冷却どちらにするかが決定されます。
ブラシ付きDCモータ
ホビー用途で使われる場合、モータ部に風が流れる構造になっている場合も多く、放熱フィンやヒートシンクを設置することで、効率的に冷却が可能です。安価に効果が得られることもあり、定番の方法です。モータ形状に合わせた専用のシートシンクなども販売されています。より強力な冷却が求められる場合、ヒートシンクに小型ファンを設置する形もポピュラーです。
ブラシレスDCモータ(BLDC)
ブラシレスDCモータは、システムに合わせたカスタムモータが設計される場合も多く、その場合は筐体内にモータドライバがセットで設置されます。
このとき、モータとドライバの両方を冷却することが必要となるため、筐体内全体の空気を押し出すことで冷却を行う方式、すなわちファンによる冷却が採用されます。ハードディスクなどはまさにこのような形であり、筐体内の熱をファンによって入れ替えることで冷却しています。
サーボモータ
サーボモータは、動き続けるモータというよりは、必要なときに必要な動きを必要なだけ行うモータのため、比較的運動量は少なめです。そのため、小型のモータであれば、冷却のための機構を設置する必要がないものもあります。
一方で、大型のサーボモータの場合は、正確な動きを実現するために急な電流値アップによる発熱などが発生するため、冷却ファンが必要な場合もあります。用途、モータのスペック、使用環境に応じて、適切な冷却を施す必要があります。
ステッピングモータ
ステッピングモータは、停止時にも電流が必要となる一面を持っており、比較的電流を流している時間が長いモータです。そのため、発熱が多くなる場面も多々あります。最近は、位置制御の優位性を利用するために、3Dプリンタに採用されることも多いのですが、基本的に冷却ファンとセットで設置されます。
いずれにしても、用途によってどのモータも発熱量は変わってきます。このモータにはこの冷却を採用すればOKということはなく、必ずご自身の用途に合わせ、適切な冷却方式の検討が必須です。
モータの熱対策でお悩みならユニテックへご相談ください
ユニテックでは、モータの使用条件に合わせた冷却方法のご提案をしております。条件を詳しくお聞かせいただければ、最適なご提案をいたします。ぜひご相談ください。ご連絡お待ちしております。